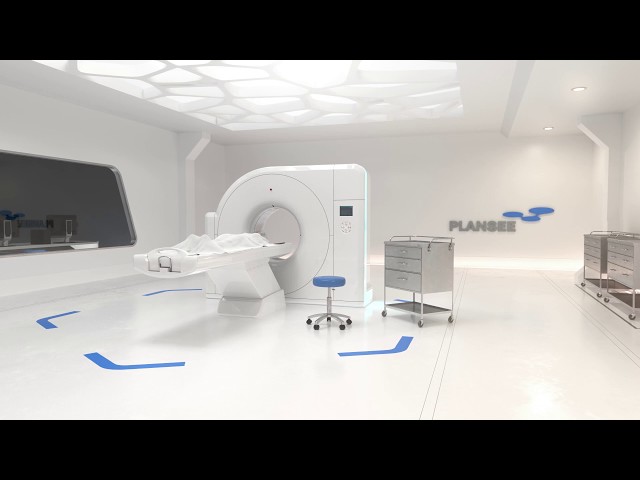
X-ray technology is being used in more and more industries; in addition to medical technology, it is also employed in security technology, quality assurance (inspection), the food industry, and measurement technology. The requirements placed on the X-ray sources for these systems are varied and require the most diverse range of technical solutions.
We use our refractory materials to produce tailor-made X-ray anodes and components for all of these X-ray tubes, which satisfy the most stringent requirements in terms of quality and precision.
REACH- and RoHS-compliant materials
Design optimizations by means of FEA
Tailored production procedures
100% product testing and tracing
Ready-to-install high-vacuum components
Management of the entire product life cycle
We provide full-metal rotating X-ray anodes and rotating X-ray anodes with a graphite body specially designed for X-ray tubes. These rotating X-ray anodes are manufactured from molybdenum alloys such as TZM, molybdenum-hafnium carbide (MHC), or molybdenum-niobium (MoNb) with focal tracks made of various tungsten-rhenium alloys. These rotating X-ray anodes can be combined with coatings and soldering solutions from our extensive technology portfolio.
We produce our stationary anodes that are back-cast with copper from tungsten, potassium-doped tungsten (WVM), or tungsten-rhenium (WRe). The perfect combination of tungsten and copper ensures excellent heat removal and guarantees a long service life of our components.
We also produce linear anodes for generating X-rays from TZM- or copper bodies with a soldered W or WRe focal track.
X-ray radiation is produced by the deceleration of free electrons at the anode. The free electrons are generated via filaments or flat emitters. Plansee has specially doped non-sag tungsten and WVM materials and semifinished products for this purpose. Secondary electrode interceptors, which we produce from forged TZM bodies, are used to intercept scattered electrons. We use materials such as Mo and Ni for the cathode holders/arms and focusing heads. The cathode components can be soldered with the ceramic insulators (for the electrical connections) to form a single assembly in a single soldering step.
We produce extremely robust drive components such as rotors, spiral groove bearing components, shafts, nuts, washers, and heat shields for high-resolution devices, from general X-rays through to computer tomography scanners.
Our drive components are made of molybdenum and tungsten as well as alloys and composites containing copper or noble metals.
We use various joining techniques for this.
During the generation of X-rays, our materials reduce environmentally harmful radiation to a minimum. Shieldings and components made of refractory metals such as tungsten, molybdenum, and tungsten heavy-metal alloys (DENSIMET®) make sure the radiation only occurs where it is actually needed.
Our materials satisfy RoHS criteria (Restriction of Hazardous Substances) and represent an alternative to components containing lead for numerous medical technology manufacturers.
The uncompromising quality and reliability of our products are essential to us. We therefore only use the purest materials and alloys for our products. From raw material supply all the way through to the finished product, we closely monitor every step in the production process. We have combined all the expertise for this under one roof. This guarantees transparent production and 100% traceability of the products for our customers.
We always inspect and package all components carefully prior to delivery. We package particularly sensitive products individually according to specific customer requirements. We even deliver high-vacuum components ready to install.