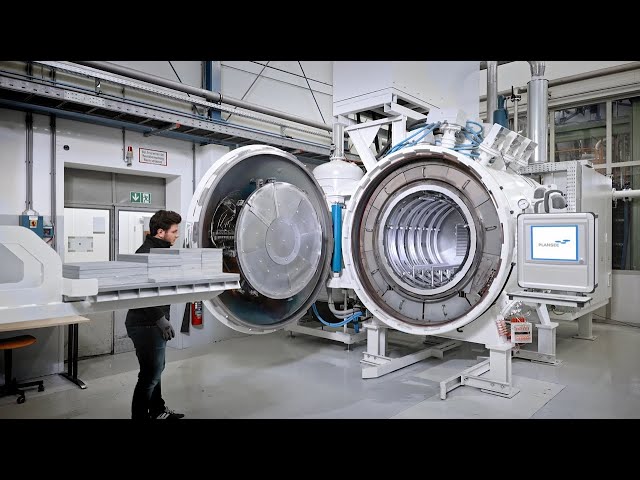
At working temperatures between 900 °C and 2800 °C, our metallic hot zones made from refractory metals are the first choice. Key factors in your high-temperature process depend directly on the hot zone, including temperature distribution, process purity, and energy consumption. For many years now, we have been reliably supplying customers all over the world with hot zones in a wide range of versions.
In addition to pure molybdenum, which guarantees optimum purity in the furnace, we also use the molybdenum alloys molybdenum-lanthanum-oxide (ML) and titanium-zirconium-molybdenum (TZM) for our hot zones. Heating elements made from these alloys are extremely dimensionally stable and strong. For particularly high operating temperatures, tungsten is the ideal material. It has the highest melting point of all metals and is therefore extremely heat-resistant.
To make our hot zones even more sustainable for use by customers, our experts are continuously working on developing the heating elements further. As a result, our hot zones are now even more efficient. Unwaveringly high stability in the high-temperature process means that, depending on the hot zone version, they require up to 37% less energy compared to industry standards. This means that they also reduce CO2 emissions in the production process.
High energy efficiency
Attractive delivery times due to standardization
Innovative standards and customer-specific designs
Efficient planning using the online configurator
Full-metal hot zones for the highest purity
All-round service, on-site and also remotely
Energy efficiency is now no longer a selectable option in our hot zone range. Instead, every variant of the new hot zone generation is geared towards maximum energy efficiency, regardless of the product line and variant you choose.
You can choose between two product lines: Basic or Premium. Our Basic line is suitable for temperature ranges up to 1350 °C, whereas our Premium line can be used for temperature ranges up to 2800 °C.
Both lines are available in a Standard or Plus variant, which differ in terms of material, design, and delivery time. Need a custom solution? Then the Plus variant with customization option is the right choice for you.
Key criteria in selecting the appropriate product line and variant:
Product line | BASIC | PREMIUM | ||
Variant | Standard | Plus | Standard | Plus |
Hot Face | Mo | Mo | ML | ML |
Sheet Design | Flat | Flat | Honeycomb | Honeycomb |
Temperature range | 900 - 1,350 °C | 900 - 1,350 °C | 900 - 1,650 °C | 900 - 2,800 °C |
Customization | Not possible | Possible | Not possible | Possible |
Delivery time | ++ | + | ++ | + |
++ shortened delivery time due to standardisation, + regular delivery time
Both the Standard and Plus variants are available in different dimensions that vary in terms of usable space and orientation: horizontal or vertical orientation, round or rectangular.
Hot zone round, horizontal positioned
Hot zone rectangular, horizontal positioned
Hot zone round, vertical positioned
To configure your Plansee hot zone and get a quote, simply use our online configurator. You can send all the relevant key data to us with just a few clicks and receive your individual quote in next to no time.
As individual as the relevant hot zone variants are, they all still have one thing in common: the highest possible efficiency. Numerous technological optimizations mean that our innovation team have succeeded in reducing energy consumption in the high-temperature process by up to 37% on average compared to the industry standard.
Your benefits are lower operating costs and reduced CO2 emissions. As a result, we are making a valuable contribution to our environment and are supporting our customers in achieving their individual sustainability goals.
As the figure shows, the Premium version of our new generation of hot zones in the Standard variant requires up to 11% less energy, and even up to 27% less energy in the Plus variant. This has been made possible through numerous innovations in the heating elements.
Our cross-divisional engineering team is a true specialist in furnace construction. Whether it's a coating system, annealing furnace, or sintering furnace, we are familiar with all high-temperature processes. Depending on the atmosphere, throughput time, and temperature, we will work with you to find the best solution for your furnace. To make sure every detail is correct in the finished hot zone, we use FE analyses to simulate the behavior of the hot zone in practice.
In the case of complex projects, our engineering team models 3D drawings on the computer. Even before it is put to use, everything is tested, right down to the last screw. Our team prides itself on finding innovative solutions for your applications. Until now, heating elements have had a planar design. With one disadvantage: these heating elements begin to sag very quickly under high temperatures in very large furnaces. This results in short-circuits, cracks, and therefore failures. The new design, patented by Plansee, is curved, thereby preventing sagging.
Whether you're working with a high vacuum, a protective gas atmosphere, or hot isostatic pressing (HIP), whether you have questions about sintering, soldering, annealing, or heating systems, we are the right manufacturer for you.
Hot zones consist of countless individual parts such as heating elements, shieldings, riveted racks, heating tapes, and rails. We offer both standard and tailor-made solutions:
WVM wire mesh heating
Riveted shielding
ML rope heating
ML sheet heating
ML/Mo sheet shielding
If your existing hot zone has become outdated or is no longer delivering the required performance, call on Plansee as a reliable partner for replacing your hot zone. We guarantee top quality and reasonable prices. Our experienced global service team will deal efficiently with your request.
Ask your system manufacturer about our hot zones. We have been working closely with furnace manufacturers throughout the world for decades and they have come to rely on our quality.
Regardless of whether you need an entire hot zone or a spare part for your existing furnace, naturally we would be happy to install our products for you on-site. Our experts can also handle the inspection, maintenance, and optimization of your existing furnaces.
Should repairs become necessary, that is also a task that we would be happy to take care of for you on-site. If desired, our experts can also provide a remote service to support your needs. The major advantage of this is that questions and problems can be answered and solved quickly, significantly minimizing your downtimes.
We produce our hot zones at various sites within our worldwide production network. With the world's largest production facilities for refractory metals and our large sales and production network, we can guarantee customer focus, reasonable prices, and sufficient capacity.
50,000 individual parts, 8 meters in length, 6 metric tons in weight. These are the dimensions of our largest hot zone. The entire manufacturing process was overseen by our team, from construction through to installation in the boiler directly on the customer's site. We even developed new tools for the demanding heating components.
In addition to our hot zones, we offer a large range of products, heating elements, and raw materials for your high-temperature process:
Is your product not yet included? Get in touch and we'll be happy to develop a tailor-made solution for your specific application.
We offer additional standard items for furnace construction as well as semifinished products in our Plansee online shop. You can quickly and easily order configurable dimensions from stock.